Industrial Metal Fabrication Is A Key Element of Modern Day Manufacturing
- By Falconics
- •
- 07 Dec, 2019
- •

What Can Be Made After Metal Fabrication?
Projects that require metal fabrication can include simple things like grills or handrailings, to the making of machinery and heavy equipment. You can make cutlery, handtools, springs, wires, screws, nuts, bolts and a lot of architectural products like roofing and cladding. The metals used in metal fabrication can be iron, steel, stainless steel, copper, bronze, brass and any other metal that can be worked on to change its configuration, shape, or thickness. This can also be achieved by forging and stamping, besides the processes referred to above.
How Is Metal Fabrication Carried Out?
Industrial metal fabrication makes for an industry that has many broad applications in many industries, both big and small. The standard raw materials in use for metal fabrication are plate metal, castings, metal that has been formed and expanded, flat metal, metal of various sections, and welding wire.
Most metal fabrication is carried out in shops where experts well versed in welding, ironwork, blacksmithy, and other professionals are employed. You will also find people who are well versed in cutting, punching, the use of press machines, machine and lathe operators, welders, assemblers, solderers, and brazers.
A Look At The Various Processes Involved
Most industrial metal fabrication will involve cutting. While the older methods used saws for this process, modern fabrication shops use water jets, plasma, and laser for the cutting. The methods used by fabricators will depend on the complexity of the cutting and its cost.
Folding is the process involved when metal parts need to be bent and most fabrication shops will use brake presses that are manually, hydraulically or motor-driven. Dies are often used for the mass production of specific forms and shapes.
Machining is a process that involves removing metal from raw metal to form specific shapes. Lathes, drills and other cutting machines are used for this.
Punching is another process that is often used in metal fabrication before assembly or metal forming. Dies are extensively used in this process. Stamping is a process similar to punching, and may not require cutting of the metal as in punching. Shearing is a process that requires cutting metal to the required size and is a process most often carried out on sheet metal.
Welding is an essential process in industrial metal fabrication and involves joining two metal pieces together by using molten metal. Welding techniques are constantly evolving and not only welding but also all processes of metal fabrication are constantly changing to suit the increasing demands for quality, speed, and economy.
The metal fabrication industry is capital intensive and machinery is becoming increasingly sophisticated as automation and CNC techniques are largely being employed. Metal fabricators have to learn to constantly change production lines as customer needs ask for diverse products that suit their specific needs.
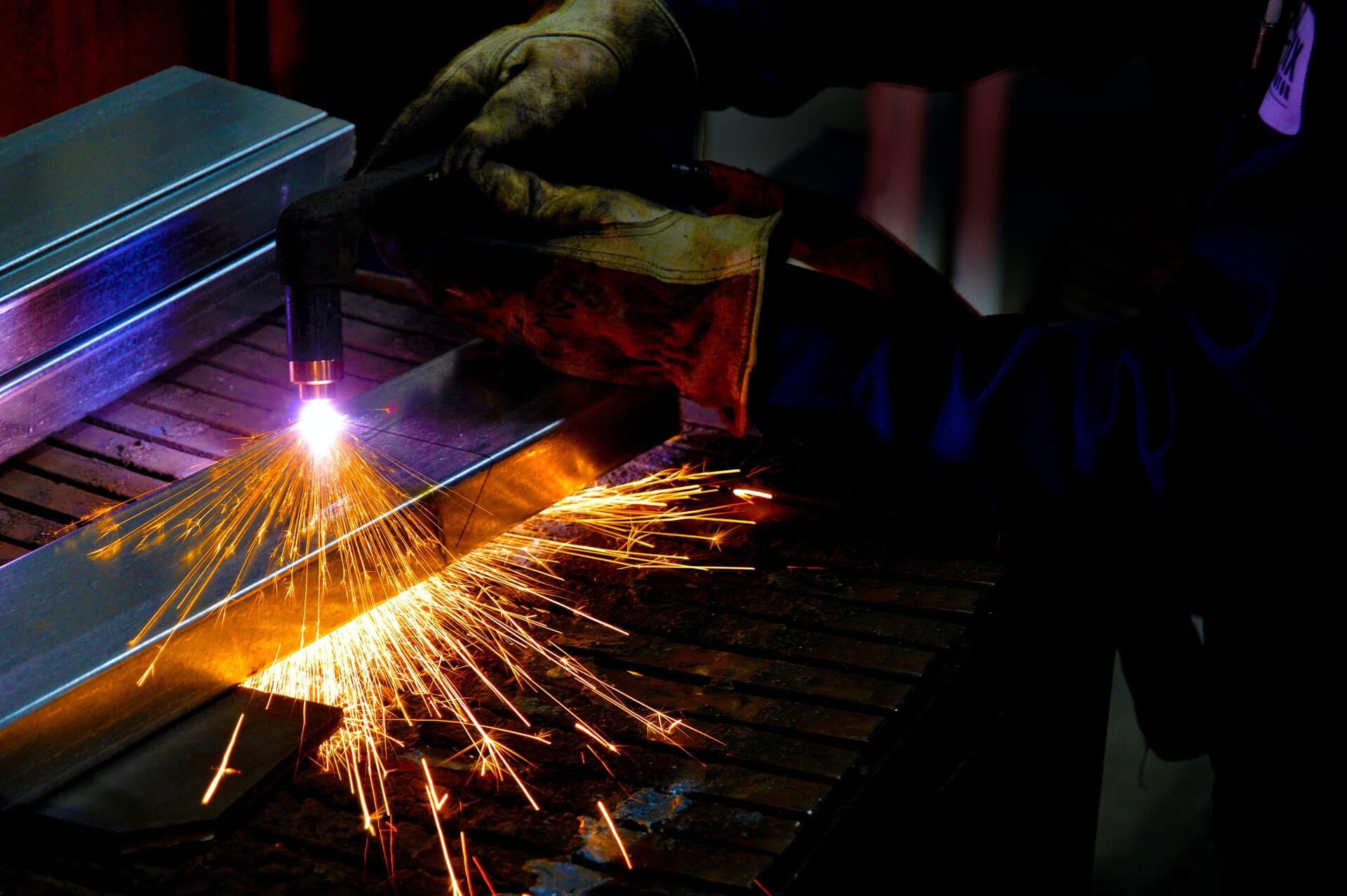
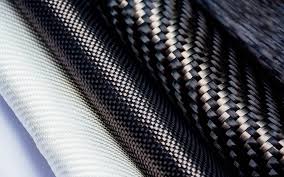
Composites are chosen by transportation and sporting industries mainly for its strength to weight ratio. It’s stronger than metal and lighter in weight, makingit a desirable material to work with.
This highly-engineered material is composed of cloth fibers and a form of resin epoxy. Although durable, there is a risk that it will be damaged by burns, saws, mills, or rout. This problem is easily solved with waterjet.
Through an easy and precise erosion process, waterjet cuts material at high speeds without heat transfer. This technique is perfect for sporting goods, composite boat hulls, and automobile components. It also includes large commercial airplane parts along with small airplane clips and parts.
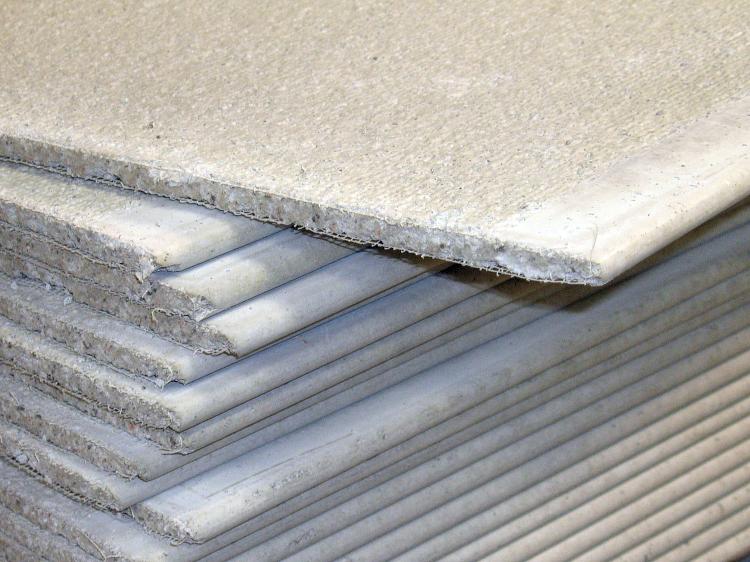